Specification:13.7mm-1219.2mm(1/4''-48'')1.5mm-60mm Standard:GB,ASAPI5Lx42,PSL1carbonsteelSLAWpipeTM,API5L,API5CT,DIN,JIS OD:13.7mm-1219.2mm(1/4''-48'') WT:1.5mm-60mm Grade:10#,20#,45#,16Mn,Q235,304L,316L,ST42,ST52,A106-a,A106-b,27SiMn,12Cr.
Steel pipe weld welding
Welding is a professional, highly normative work in the steel construction is very important, therefore, as a key in the bridge steel arch ribs processing monitor the entire process.
4.1.1 welding preparation
Construction technology department in accordance with the design documents, refer to the relevant standards, norms, procedures, and to develop the principle of welding process, a clear welding method, process measures, quality standards and acceptance norms. The bridge's arch rib pipe welding methods are manual metal arc welding, CO2 gas shielded arc welding, submerged arc welding.
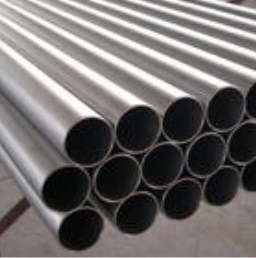
Process Assessment: the welding procedure qualification based on steel manufacturing, construction units must be combined with engineering complete process evaluation documents and completion of the file reference purposes. Butt, lap weld in the form of the T-shaped connector to determine the appropriate welding methods are not free to change.
Before welding processing: groove weld all components and positive and negative 25mm range, should be required to clean up and remove surface oil, rust, oxide and dust pollution, handle clean before welding ceramic backing must be rules for the operation construction.
Production test panels: To ensure that the weld quality, the South River Bridge Rib structure located production test panels, test panels and the corresponding weld the same material, same thickness, the groove, with the rolling direction, and the corresponding technical standards to do the mechanical properties test to ensure that its parameters to meet the specification requirements. Development of production test board evaluation process ", the purpose, scope of application, reference standards, and technology content to make specific provisions to ensure that the quality of welds.
4.1.2 The welding requirements
Factory welds: South River Bridge arch rib steel pipe production, assembly, and its vertical joints, circumferential seam of the v-groove, single-sided welding sided forming negative (tube) attached to a ceramic backing. Seam filling process is divided into four, CO2 gas shielded welding primer to fill two automatic submerged arc welding to fill one, to cover up one. The beginning and ending end of the longitudinal seam welding arc plates were installed and put out the arc plate, groove type longitudinal seam. Girth welding rolling tire rack, welding temperature welding manner. Each process to weld once, for some reason stopped welding and continued welding arc from the parent material shall not arc at the gas must be planed or polished into a 1:4 slope lap, lap length not less than 50mm.
Site installation: site installation manual arc welding, wind bracing and Rib wind bracing between the intersecting line segments docking symmetrical welding. Rib Closure Segment, position, subject to meet the design close temperature before welding.
4.1.3 The weld quality inspection
South River Bridge weld grade requirements to reach the GB50205 Class I weld requirements. Weld appearance quality requirements, forming beautiful, neat size to comply with the design and process requirements, so that no cracks, no pores, slag, welding tumor, no crater and weld defects. Its intrinsic quality requirements in the 24 hours after the completion of the weld, ultrasonic testing 100% of the weld length, 10% do the testing and inspection of the X-ray.
4.2 linear processing
Rib segment is the basic unit of the formation of the arch axis, depending on its linear segment Rib pipe fire workers microbending. Pyrotechnics the microbending method is to fire workers and the external formation of the design curve. Calculated by computer according to the design of arch axis equation to determine the coordinates of all the control points of the segmented upper and lower arch rib steel pipe, as the basis of the microbending and monitoring and control, process documents and the preparation of specific acceptance criteria.
Implementation steps: marked its vertical and horizontal centerline and auxiliary line design and construction of the model tire rack → → determine the location of the tire rack each station line, accurate installation imposition of external support equipment → Rib pipe in place, set the plane coordinate → draw plus tropical → points with heating pushes.
Control points:
(1) to ensure correct positioning of the steel pipe to be bent on tire rack, steel radial center line should be consistent with the tire frame longitudinal centerline and midline;
(2) heating from both ends to the central symmetry;
(3) The external force is reasonable point to be symmetrical, the pressure should be gradually, moderate;
(4) with particular emphasis on coordination and control of pressure and temperature;
(5) and should avoid tropical circumferential seam location, agreed bandwidth according to the actual appropriate adjustments;
(6) to be observed at any time, measuring the coordinates of the arch axis, control near a bend.
4.3 Rib pre-fight
Rib molding meets the linear design is the key bridge, arch rib segments produced to complete required pre-fight of its span, arch axis, accurate level degrees (lateral shift of the arch axis) and the boom position comprehensive inspection, hoisting the site to prepare. South River Bridge Rib factory pre-fight with horizontal whole piece of pre-fight program.
Way pre-fight: lifting the order in full accordance with the segment site, by the arch of the foot embedded segment, since both ends of the symmetry, close the segment retained segment production margin (Subject to the site installation and removal), other segmental resection production margin (retaining only the circumferential seam gap margin).
Control points:
(1) rigid enough flat space, space, equipped with the appropriate lifting equipment, tire rack tooling, etc.
(2) detection equipment to send a special unit of measurement calibration.
(3) preparation of a good pre-fight process to develop the pre-fight program.
(4) The pre-fight program pre-fight, take good care of the pre-fight measurement data, and to take certain measures to protect the pre-fight control points, used to prepare the installation.
Factory pre-fight, to detect the machining accuracy of the arch rib segments, to eliminate the processing deviation of the arch rib segments to complete the preparatory work for construction site lifting.
.
Related post
Archives
-
Seamless steel pipe
- Line pipe
- OCTG pipe
- Mechanical steel pipe
- Structural steel pipe
- Boiler Tube
- ERW pipe
- SSAW pipe
- LSAW pipe
- Corrosion protection pipe
- Insulated pipe
- Abrasion resistant pipe
- Stainless steel pipe
- API pipe
- ASTM pipe
- Galvanized steel pipe
- Water pipe
- Gas pipe
- Carbon steel pipe
- Alloy steel pipe
- Hot rolled pipe
- black steel pipe
- Flange
Welded steel pipe
Special steel pipe
Pipes
Pipe Fittings
3 Comments
straight seam welded steel pipe, ASTM straight seam welded steel pipe,OD:203-820mm WT:3.5-35mm,Certification:ISO9002, ISO9001-2000,API 5L API 5CT TS16949.
DIN1629 seamless steel pipe ,DIN1629 ST37 steel pipe,2material:20#,45#,ST37,S45C 3high quality,best price 4Key word:steel pipe 5best price.
API 5CT Oil Pipe,We can supply full range of seamless carbon steel pipes and tubes which can not be supplied by any of the manufacturers alone. And API 5CT J55,API 5CT N80 is our mainly products.Seeing is believeing,we sincerely invite you t.
DIN2391 steel pipe,DIN 2391 carbon steel pipe,DIN 2391 St45 Seamless Steel Pipe Usage: Applicable to transport liquid, gas, oil etc..
ASTM A335 P22 alloy pipe,alloy seamless steel pipe,Alloy steel seamless pipe/alloy pipe/alloy steel pipe/high-temperature alloy steel pipe/ alloy tube/ASTMA335 standard alloy pipe P22/ ASTM A335 P22 alloy pipe, alloy seamless pipe p22,Q345A/.
DIN1629 St52 seamless pipe,PRODUCTS: DIN1629 St52 seamless pipe, DIN1629 St52 seamless steel pipe, DIN1629 St52 seamless tube, DIN1629 St52 seamless steel tube.